Efficienza, resilienza, rapidità, precisione. Sono solo alcuni tra i requisiti essenziali che si richiedono al mondo delle macchine agricole. Questo è il settore nel quale le stagioni la fanno da padrone ed è imprescindibile disporre di macchine e attrezzature pienamente funzionanti. Ogni ritardo, intoppo od ostacolo comporta inevitabili rimesse, sia quelle dovute all’inattività sia quelle necessarie alla risoluzione del problema. L’imprevisto, d’altro canto, si presenta immancabilmente e, per definizione, quando meno te lo aspetti.
Queste dinamiche sono ancor più vere se applicate al settore dei trattori agricoli, le potenti motrici che sostengono la stragrande maggioranza delle attività svolte in campo. Sono veicoli estremamente complessi che gestiscono turni di lavoro lunghi ed intensi e operano in condizioni di esercizio gravose, che ne sollecitano i numerosi sottosistemi. Non stupisce quindi che queste macchine, proprio come noi umani, subiscano un progressivo processo di invecchiamento che rende via via più necessario il controllo dello stato di salute attraverso un insieme di attività manutentive.

Tre tipologie esistenti
La manutenzione, intesa come azione di monitoraggio della salute e risoluzione di eventuali criticità, comprende un ampio ventaglio di soluzioni e può essere categorizzata come reattiva, quando viene eseguita in seguito al verificarsi di un evento critico (rottura di un componente, avaria di un sistema ecc.), oppure preventiva, qualora consista in un insieme di azioni programmate che utilizzatore (manutenzione ordinaria) e personale qualificato (manutenzione generale) devono periodicamente svolgere. Infine, può essere predittiva quando è eseguita solo immediatamente prima che una criticità si manifesti.
Il primo tipo di manutenzione risulta conveniente solo al verificarsi della rottura di quella componentistica velocemente riparabile o sostituibile che non comporta un fermo del mezzo. D’altro canto, manutenzione preventiva e predittiva parrebbero gli approcci più interessanti per il settore delle macchine agricole poiché, rispettivamente, limitano ed eliminano il tempo morto durante il quale la macchina non è produttiva. Fanno parte dell’approccio preventivo le classiche (ma importanti) azioni di controllo come quelle eseguite all’olio motore, all’olio del circuito idraulico, al filtro dell’aria e così via. Per tutte quelle azioni che non rientrano nella categoria della manutenzione ordinaria occorre fare visita a un centro tecnico certificato.
L’approccio preventivo risulta una combinazione di manutenzione ordinaria e generale che oggigiorno può essere facilmente gestita dai numerosi programmi manutentivi resi disponibili dalle case costruttrici di macchine agricole. Scopo di quest’approccio risulta essere l’esecuzione di ispezioni e azioni pianificate che individuino piccoli problemi e li risolvano prima che evolvano o l’attuazione della sostituzione di alcuni componenti dopo un prestabilito numero di ore di utilizzo. Esempio di programma esclusivamente dedicato al monitoraggio e all’azione manutentiva è il John Deere Connected Support, con il quale il costruttore statunitense garantisce un servizio di diagnostica e assistenza, ma anche supporto alla programmazione della manutenzione, da remoto. Questa strategia, dichiara John Deere, consente una riduzione media del tempo di diagnosi e riparazione del 20%, garantendo quindi un tempo operativo maggiore.
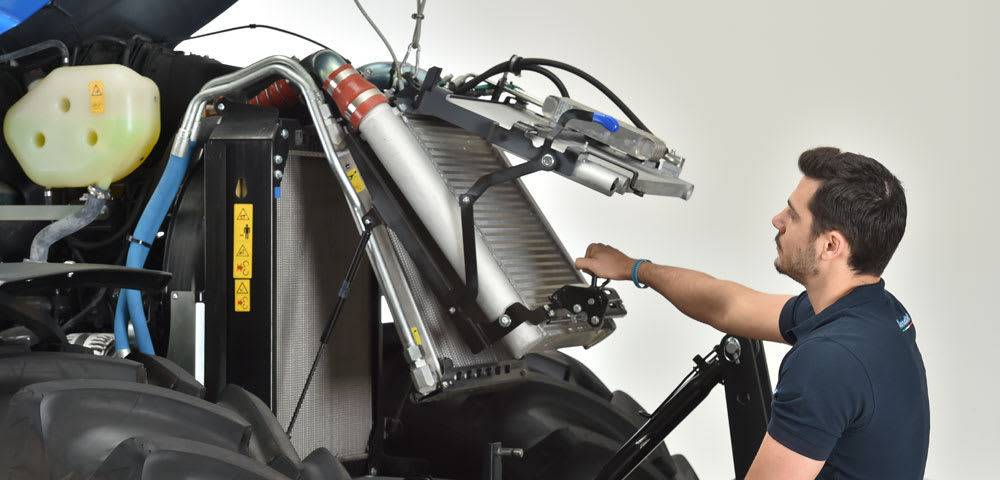
Sistemi integrati
Un aspetto innovativo introdotto dalle case costruttrici è, infatti, rappresentato dall’integrazione dei suddetti programmi manutentivi con un robusto sistema di raccolta e interpretazione di dati provenienti dalla macchina dell’utilizzatore. Questi sistemi consentono un monitoraggio da remoto istante per istante, che raccoglie dati di performance della macchina impiegati per pianificare decisioni operative. L’approccio manutentivo preventivo rimane quindi programmato, ma è supportato da dati reali. Fa parte di questa categoria il supporto AFS Connect di Case IH, ma anche l’insieme di servizi “Uptime” messi a disposizione da New Holland in combinazione con MyPLM Connect. Per quest’ultimo costruttore l’integrazione di Uptime Service con i dati provenienti dalla tecnologia PLM permette un controllo totale delle macchine connesse, una programmazione efficace delle fasi manutentive ed una gestione rapida ed efficiente in caso di guasto grazie al supporto fornito dalla Control Room di New Holland.
Ulteriori esempi fra i numerosi sistemi preventivi integrati sono le piattaforme Fendt Connect, Valtra Connect e Massey Ferguson Connect (Agco Corporation), che presentano funzionalità simili e, ancora, il servizio MyLandini del gruppo Argo Tractors e la piattaforma SDF Data Platform del costruttore Same Deutz-Fahr. Claas ha invece realizzato il sistema Telematics, mentre Kubota ha sviluppato un servizio equivalente in collaborazione con Kverneland. Tutti questi sistemi dialogano con la telemetria del mezzo e consentono una gestione ideale della macchina tramite la raccolta e l’analisi di dati reali. Tali dati sono in seguito impiegati per ottimizzare le condizioni di utilizzo, minimizzare il tempo di inattività, notificare messaggi di alert e pianificare la manutenzione in maniera intelligente, ovvero lontano dai periodi di grande attività della macchina. Questi servizi sono solitamente resi disponibili con servizi di abbonamento, come MF Connect, fornito di serie per cinque anni su tutti i trattori a sei cilindri.
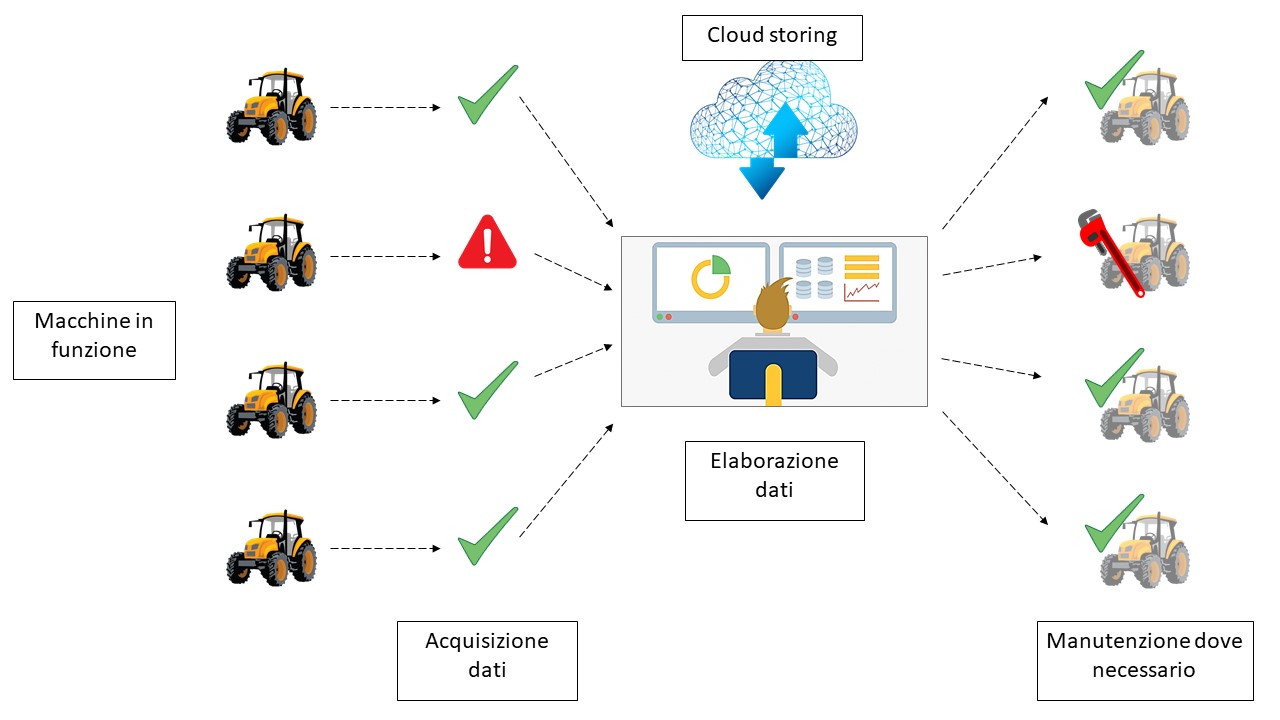
Manutenzione predittiva in crescita
Il metodo preventivo è senz’altro efficace, ma può determinare una fonte di spesa non necessaria, ad esempio quando si esegue una sostituzione programmata di un componente ben prima del raggiungimento del suo fine vita. È per questo motivo che in tempi recenti la manutenzione predittiva ha destato sempre maggior interesse. Essa viene eseguita solo immediatamente prima che una vera criticità si manifesti, evitando il fermo macchina e nel contempo la sostituzione di un componente avente ancora vita utile a diposizione. Ci chiediamo quindi come sia possibile prevedere quando un problema si presenterà, per agire anticipatamente ad esso.
La risposta può essere nuovamente trovata nell’impiego di dati dal mondo reale. L’importanza di strutturare processi decisionali basati sui dati è diventata sempre più evidente agli occhi dei costruttori e diverse strategie sono al momento in fase esplorativa.
Per strutturare questi processi decisionali non è più sufficiente raccogliere i dati di una singola macchina, ma risulta essenziale collezionare con continuità le informazioni operative di tutte le macchine vendute per poi procedere con un’analisi sistematica. Quest’analisi deve essere in grado di individuare sia le condizioni di funzionamento normali delle macchine, sia quelle anomale e, cosa più importante, deve identificare e caratterizzare i fenomeni che hanno prodotto la transizione da funzionamento corretto a critico (tramite impiego di Intelligenza Artificiale). A questo punto si dispone di una chiave di lettura dell’immenso flusso di dati giornalmente in arrivo dalle macchine degli utilizzatori: le informazioni provenienti da una macchina vengono analizzate alla ricerca di indizi che evidenzino come qualche guasto stia per accadere e in caso di riscontro positivo l’utilizzatore viene immediatamente avvertito.
Un aspetto innovativo introdotto dalle case costruttrici è rappresentato dall’integrazione dei programmi manutentivi con un robusto sistema di raccolta e interpretazione di dati provenienti dalla macchina dell’utilizzatore. Tra questi segnaliamo: Operations Center di John Deere (a), AFS Connect di Case IH (b), Fendt Connect (c), Valtra Connect (d), MyPLM Connect di New Holland (e), Massey Ferguson Connect (f), MyLandini del gruppo Argo Tractors (g), la piattaforma SDF Data Platform (h) e Claas Telematics (i)
Soluzioni ibride
Un grande attore nello scenario della manutenzione smart è sicuramente John Deere, con investimenti sempre più importanti nel mondo dei Big Data in molti settori del proprio business. In tempi recenti ha intrapreso un percorso di studio degli approcci di manutenzione predittiva, ma nessun servizio per il settore macchine agricole è stato ancora sviluppato e rilasciato. Esistono tuttavia alcuni servizi ibridi di grande interesse, che combinano aspetti di manutenzione reattiva e preventiva, ma sfruttano dati condivisi come nel caso dell’approccio predittivo. Meritevole di menzione è sicuramente il programma di controllo messo in atto per il settore “Construction and Forestry” della compagnia. Le macchine John Deere Construction sono infatti equipaggiate di sistemi telemetrici in grado di dialogare in diretta con sistemi di immagazzinamento dati in Cloud dove informazioni come posizione, ore di utilizzo, impiego in idle, temperature dei sistemi e consumi vengono stoccate, per poi essere inviate al Machine Health Monitoring Center di John Deere in Iowa (Usa). Qui il codice diagnostico in arrivo viene analizzato e, in caso una problematica sia rilevata, il concessionario locale John Deere fornisce immediato supporto. Se il problema rilevato ha già determinato un impedimento nell’operatività della macchina, John Deere invia la soluzione più adatta: talvolta un aggiornamento software, talvolta la sostituzione di un componente ad opera di un tecnico specializzato. Al di là dell’aspetto di manutenzione reattiva, il Monitoring Center svolge la ben più importante attività preventiva attraverso l’accumulo di dati dalle flotte connesse in tutto il mondo in modo tale che se un particolare problema si manifesta in maniera sistemica su diverse macchine allora si individua questa tendenza nei dati e il Monitoring Center sviluppa una strategia risolutiva. Quest’ultima può essere erogata direttamente al consumatore e contemporaneamente condivisa con il settore progettuale John Deere in modo da porre rimedio al problema direttamente sulla linea produttiva delle macchine.
In definitiva, sebbene l’approccio predittivo sia una tecnica complessa e richiedente ingenti risorse al costruttore, presenta comunque un elevato potenziale in termini di abbattimento di costi ordinari e straordinari, sia per l’utilizzatore finale sia per il costruttore stesso. Possiamo pertanto aspettarci un improvviso impulso verso la manutenzione predittiva anche per il settore del farm machinery? Ma soprattutto, considerati i cicli di lavoro stagionali propri di queste macchine, ha senso un investimento in tale direzione che assicuri un controllo così capillare? Staremo a vedere.
Utilizzo dei dati?
• Analisi dati di posizione, consumo, temperature, codici di errore in tempo reale: individuare rapidamente possibili anomalie prima che degenerino in problemi operativi.
• In caso di problemi operativi: dati impiegati per l’analisi remota rendendo possibile un rapido intervento mirato.
• Ricerca di criticità sistematiche nelle flotte: individuazione ed eventuale correzione progettuale.
L'autore è del Distal - Università di Bologna