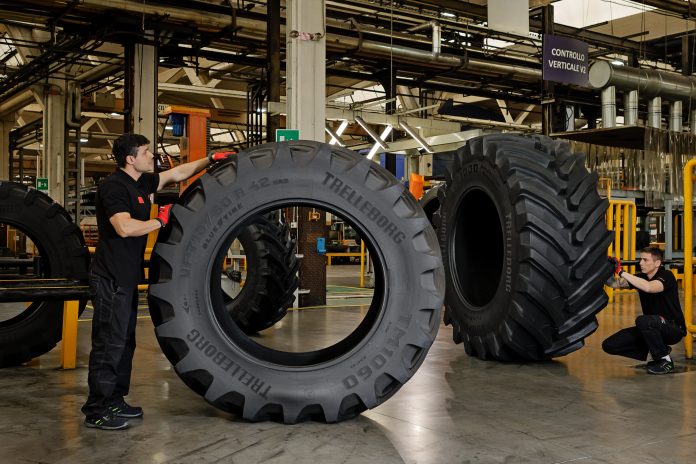
Di stabilimenti industriali circondati da un oliveto con 500 piante quasi secolari non ne esistono tanti. Anzi, probabilmente ne esiste uno solo e si trova a Tivoli (Roma), tra l’altro a meno di un chilometro da un sito archeologico come Villa Adriana. Stiamo parlando dell’Headquarter Globale Yokohama TWS, al cui interno si trova il sito produttivo Trelleborg Tires, che ha radici veramente lontane nel tempo, dal momento che è stato costruito nel 1934.
«La prima azienda che lavorava qui si chiamava I.A.C. (Industria Articoli Caucciù) – ci racconta Valerio Cacioni, Plant Manager di Trelleborg Tires – attiva fino al 1938, anno in cui venne acquistata da Pirelli. Pirelli ha posseduto lo stabilimento fino al 1999, producendo sempre pneumatici per l’agricoltura, a parte un periodo in cui produsse anche pneumatici Passenger negli anni 70. Negli anni ‘90 lo stabilimento si trovò a fronteggiare un cambiamento significativo, con un progressivo disinvestimento di Pirelli sulla fabbrica e sul settore agricolo. Fu nel 1999 che il sito assunse una nuova direzione, entrando a far parte di un gruppo che lo avrebbe portato a diventare uno degli impianti di riferimento per la produzione degli pneumatici Trelleborg Tires a livello globale.».
Nel decennio successivo all’acquisizione il sito ha vissuto una fase di evoluzione, durante la quale il brand Trelleborg Tires ha progressivamente affermato la propria identità nel mercato degli pneumatici agricoli. Da allora a oggi lo stabilimento ha cambiato faccia, arrivando a produrre un mix sempre più spinto verso misure extra large in agricoltura. Dopo l’acquisizione e l’entrata nel Gruppo Yokohama Rubber Co. nel 2023, oggi l’azienda si chiama Yokohama TWS e oltre a Tivoli comprende altri 13 stabilimenti, che producono sia a marchio Trelleborg sia a marchio Mitas, Maximo e Cultor.
«Da Tivoli escono solo pneumatici marchiati Trelleborg – precisa Cacioni – abbiamo una sala mescole nostra e produciamo su un mix produttivo abbastanza spinto in termini di misure. La maggior parte della produzione di Tivoli è destinata agli Oem (Original Equipment Manufacturer), ossia ai produttori di macchine agricole. Geograficamente parlando, il mercato principale è rappresentato dall’Europa Centrale, un’area strategica dove la vicinanza al cliente e la capacità di adattarsi alle specifiche esigenze locali sono elementi fondamentali del nostro approccio. La sede si estende su circa 200.000 m² e, oltre allo stabilimento, ospita anche l’Headquarters globale di Yokohama TWS, il centro globale di R&D e un Hub logistico a supporto del mercato centrale. La sede impiega circa 750 persone, di cui 500 dedicate esclusivamente alla fabbrica.
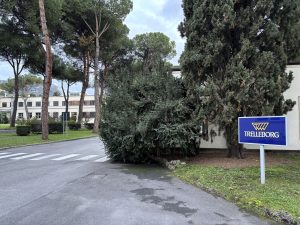
Cinque fasi fondamentali della produzione
Le principali fasi di produzione dello pneumatico sono cinque: produzione della mescola, realizzazione dei semilavorati, assemblaggio (o confezionamento, dove i vari componenti di mescola lavorati nel reparto semilavorati vengono assemblati), vulcanizzazione (tramite presse che “cuociono” lo pneumatico “crudo” appena assemblato) e infine finitura, durante la quale lo pneumatico viene controllato e si effettuano tutti i test di qualità per garantire al cliente il top dal punto di vista della performance.
«La qualità del prodotto è garantita fin dalle prime fasi produttive – spiega Cacioni –. Le materie prime e le mescole sono attentamente controllate attraverso i laboratori condivisi con il centro di R&D dei materiali. Questa sinergia rappresenta una grande opportunità per il nostro stabilimento: avere il centro globale di ricerca e sviluppo dei materiali nella stessa sede consente un continuo scambio di know-how e best practice con il reparto mescole, rafforzando ulteriormente il nostro impegno verso l’innovazione e l’eccellenza.».
Gli ingredienti che portano alla produzione della mescola sono ben visibili nello stabilimento tiburtino e raccontano come può essere composta la mescola a partire dalla materia prima: gomma naturale, gomme sintetiche, carbon black, attivatori che ritardano o accelerano la vulcanizzazione durante tutto il processo, e ovviamente zolfo, elemento essenziale nel processo di vulcanizzazione. «Nonostante sembri un unico pezzo nero, in realtà lo pneumatico ha diversi componenti – sottolinea Cacioni – partendo dalla parte più visibile, la fascia battistrada, per arrivare al fianco, al cerchietto (la parte di contatto con il cerchio), alle cinture e alle tele interne. Ecco, ognuno di questi componenti ha almeno una mescola diversa rispetto agli altri per garantire da un punto di vista meccanico le giuste performance».
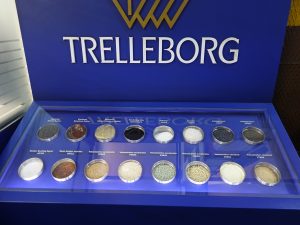
Solo tessuto, niente acciaio
In questa fase emerge già una particolarità dello stabilimento di Tivoli. «Per quanto riguarda la produzione della carcassa, che rappresenta la parte centrale del prodotto – continua Cacioni – a Tivoli produciamo solamente in tessuto. L’acciaio lo utilizziamo solo nei cerchietti, il componente che dovrà garantire l’adesione al cerchio, perché la morbidità tipica del tessuto consente di avere quell’effetto galleggiamento sul campo che fa la differenza lavorando a pressioni molto basse, riducendo il calpestamento del suolo grazie a un’impronta più ampia e aumentando quindi la produttività. È chiaro che, a seconda della tipologia di applicazione e di ruota, possono essere preferibili le cinture in acciaio che vengono utilizzate in altri nostri stabilimenti».
La miscelazione avviene in macchine a sviluppo verticale, per cui si parte dal deposito di carbon black che per gravità viene inserito all’interno del miscelatore, nel piano intermedio entrano le gomme naturali e sintetiche e i prodotti chimici, e poi c’è il deposito oli all’esterno. Finita la miscelazione, la mescola tramite un estrusore e una calandra prende la forma finale, viene raffreddata e stoccata all’interno dei pallet. A fine linea la mescola viene sottoposta a valutazione reometrica e, se i parametri sono corretti, potrà essere rilasciata.
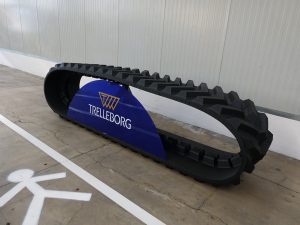
Il confezionamento
Nel nostro tour non abbiamo visitato il reparto dove lavorano trafile, calandre e macchine tagliatela, ma siamo passati direttamente a quello dell’assemblaggio (o confezione, come si usa nel gergo delle gomme), dove spiccano all’ingresso due delle tante confezionatrici per produrre l’alto di gamma di Trelleborg Tires, cioè le coperture che si aggirano dai 300 ai 600 kg di peso, tra cui anche il top di gamma TM1000 ProgressiveTraction VF 900/65R46.
«Nel corso degli anni, Tivoli ha saputo sviluppare e implementare le tecnologie produttive più avanzate per la produzione di pneumatici agricoli XL – prosegue Cacioni –. Numerosi sono gli accorgimenti di processo che, grazie a un costante perfezionamento, hanno consentito di ottenere prestazioni eccellenti, partendo dalla fase di produzione della cosiddetta “green tire” (lo pneumatico prima della vulcanizzazione).
Per il tipo di prodotto che realizziamo, è cruciale il giusto equilibrio tra fasi completamente automatizzate e processi che valorizzano il know-how degli operatori altamente specializzati. Solo attraverso questa sinergia siamo in grado di coniugare qualità, produttività e adattabilità al mix produttivo, quest’ultima particolarmente importante, considerando che il numero di tipologie di prodotto realizzate in un singolo turno può superare il numero di macchine dedicate a ciascun range di produzione, richiedendo rapidi riattrezzaggi delle linee. L’automazione rappresenta un valore fondamentale nelle fasi più critiche del processo di confezionamento, garantendo il rispetto degli elevati standard qualitativi. In queste fasi, l’affidabilità è assicurata grazie all’impiego di robot avanzati e sensori di precisione, che permettono di monitorare e ottimizzare costantemente ogni aspetto del processo produttivo».
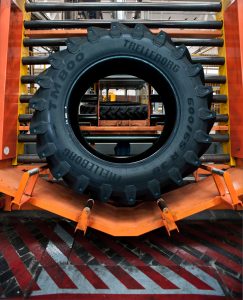
Vulcanizzazione e finitura
Segue quindi la vulcanizzazione, dove nelle presse più grandi viene utilizzato anche l’azoto oltre al vapore. «In questo stabilimento disponiamo di diverse linee di vulcanizzazione che garantiscono una produzione giornaliera continua ed efficiente – conclude Cacioni –. A differenza di quanto avviene per gli pneumatici da vettura, il ciclo di vulcanizzazione per gli pneumatici agricoli ha una durata più elevata, dell’ordine delle due ore. In questa fase così cruciale possiamo monitorare in tempo reale tutti i parametri del processo di vulcanizzazione, associandoli al prodotto finito tramite sistemi avanzati di tracciabilità integrata, che assicurano la massima precisione e affidabilità del risultato. Infine, la finitura, molto importante perché, dopo la finitura, il controllo lo fa il cliente, che per noi vuol dire nell’80% dei casi l’Oem, che ha un’attenzione molto alta verso l’estetica del prodotto.
Perciò in questa fase effettuiamo controlli visivi e ispettivi, che vengono svolti anche in magazzino con una macchina per la valutazione della radial run-out della copertura. Solo i prodotti che superano questi rigorosi controlli di qualità possono lasciare la fabbrica, arrivare al magazzino finale e, successivamente, ai nostri clienti. Oltre alla costante ricerca di un miglioramento continuo della qualità del prodotto finito, il personale tecnico dello stabilimento si dedica incessantemente all’ottimizzazione degli indicatori di qualità interna e alla riduzione degli scarti. In stabilimenti che producono prodotti di grandi dimensioni, la sostenibilità si persegue anche attraverso l’eccellenza nella gestione dei materiali e nell’efficienza dei processi produttivi».