Quando, a fine Ottocento, i fratelli Holt si apprestarono a costruire le prime motrici a vapore, a partire da una locomotiva ferroviaria, si resero subito conto che il veicolo non avrebbe mai potuto essere usato sul soffice suolo agricolo, nonostante tutti i tentativi di alleggerirlo. Se la locomotiva può correre su qualunque terreno senza sprofondare è solo grazie alle rotaie, un elemento portante liscio e capace di ridurre al minimo l’attrito, in grado di ripartire il carico su una superficie abbastanza ampia, per mezzo delle traversine. Perché, si chiesero quei pionieri, non costruire una rotaia “mobile”, che potesse essere stesa sotto alle ruote e recuperata dopo che il veicolo era passato, ricominciando il ciclo?
Da questa idea nacque il cingolo metallico, subito brevettato per impieghi civili e militari: una soluzione che ha avuto grande fortuna per i veicoli non stradali più pesanti o che devono sviluppare il massimo sforzo di trazione su terreno soffice o irregolare. Il carro rigido ha però il difetto di non adattarsi al profilo superficiale del suolo e non consente velocità elevate, al punto da consigliare l’impiego di rulli di appoggio articolati, come nei mezzi militari e in quelli da essi derivati, come i “carrier” per la movimentazione in cantiere. I cingoli di questo tipo non sono particolarmente durevoli e sono soggetti a turni di sostituzione piuttosto frequenti (dell’ordine delle centinaia di ore) rispetto al carro rigido impiegato in agricoltura e nei cantieri, capace di durare migliaia di ore.
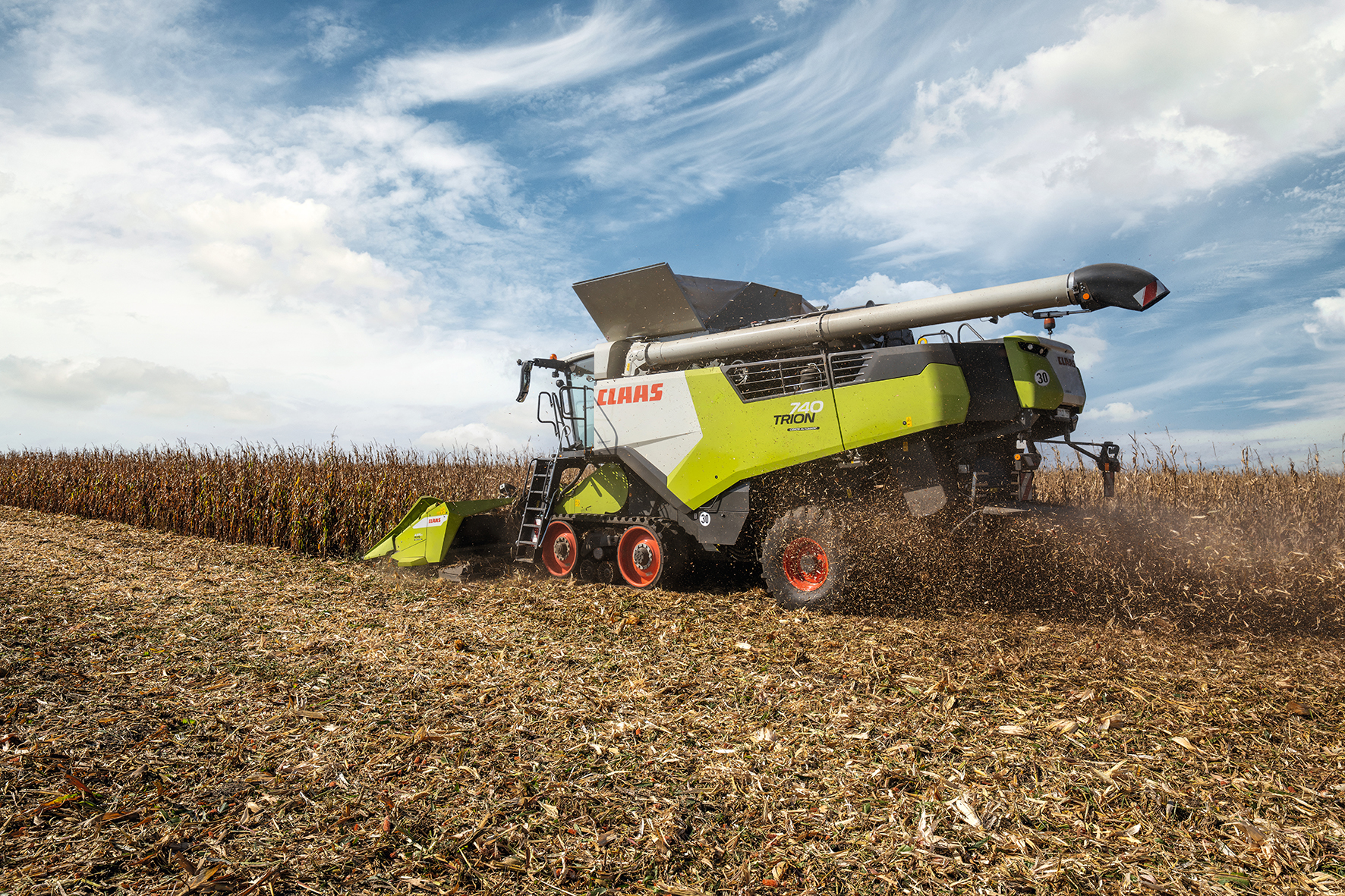
L’arrivo del cingolo in gomma
La vera rivoluzione nasce, alla fine degli anni Ottanta, con il cingolo in gomma: alla tradizionale catenaria articolata si sostituisce una serie di anelli di nastro di acciaio, annegati in una fusione di gomma con un profilo interno che impegna la ruota di trazione. Il nastro portante, flessibile ma virtualmente inestensibile, costituisce il piano di appoggio su cui è applicato il battistrada: questo ha un profilo simmetrico rispetto alla direzione solo nei mezzi da cantiere, mentre in agricoltura si usa il profilo a “v” per consentire lo scarico laterale della terra.
L’evoluzione tecnica ha aumentato considerevolmente, rispetto alle prime versioni, la durata del nastro e del battistrada, la velocità e la potenza trasmessa: nonostante tutti i miglioramenti, però, lo sforzo di trazione è minore rispetto a una catenaria metallica. La sua struttura interna rende infatti il cingolo molto “rigido”, a differenza di uno pneumatico, che può deformarsi per sopportare uno sforzo torsionale improvviso, fino a ruotare rispetto al cerchio. Sforzo che si trasmette sulla catena cinematica provocando, nelle prime versioni, avarie più o meno gravi ai riduttori e al cambio; in seguito, la progettazione integrata di tutti i componenti ha permesso di superare questi inconvenienti legati, bisogna dirlo, a un impiego scorretto del cingolato.
Nell’immaginario collettivo il concetto di “trattore cingolato” ha preso il sopravvento sulle sue caratteristiche operative, come leggerezza, velocità, silenziosità e riduzione di attriti e vibrazioni; una cosa ben diversa dal solido, ma lento e rumoroso, cingolato metallico.
Ancor oggi c’è chi impiega il cingolato in gomma per fare lavorazioni inadatte per questo tipo di veicolo, i cui pregi sono legati alla riduzione del calpestamento e all’operatività: grazie al minimo carico unitario, può entrare in campo anche su suolo umido, con la stessa velocità del gommato.
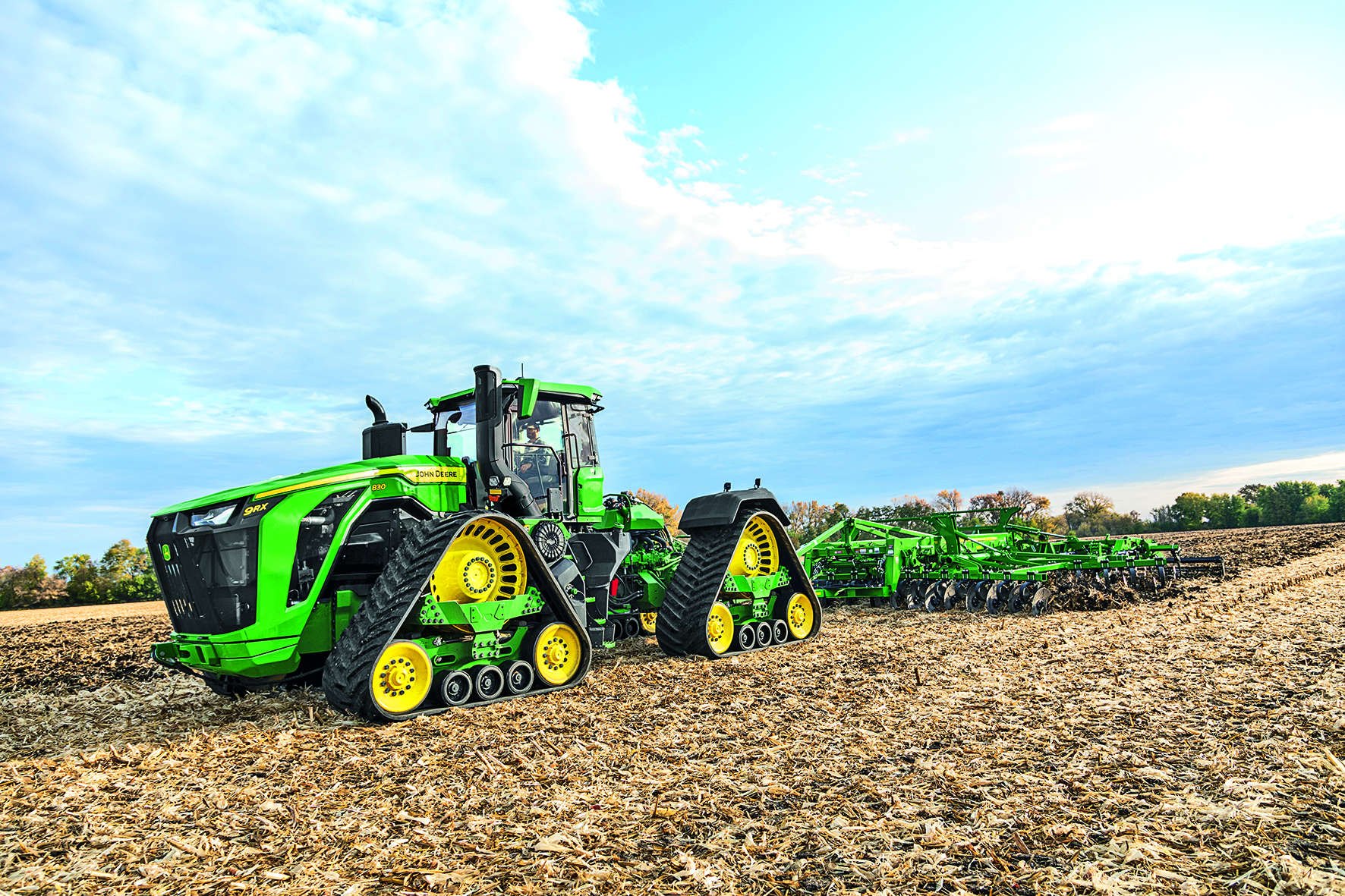
Il limite della struttura
Il cingolo ha tuttavia un limite, insito nella sua struttura: in presenza di dossi o altri ostacoli ha la tendenza a “ricadere” dopo che il suo baricentro ha superato il punto più alto: nonostante l’impiego di sospensioni sofisticate, rimane sempre un certo beccheggio che limita la velocità. Una tendenza che non ha invece il veicolo a ruote (ad almeno 2 assi), la cui struttura consente di assorbire e limitare le oscillazioni longitudinali: una considerazione che sta alla base delle soluzioni a 4 cingoli o nei semicingolati, che stanno prendendo piede sulle grandi potenze.
Un’altra caratteristica del cingolo risiede nel fatto che lo sforzo di trazione è direttamente proporzionale alla superficie di contatto con il suolo: il cingolo raggiunge il massimo rendimento solo se il peso aderente è ben distribuito sulla lunghezza del nastro. Se perde aderenza sulla parte anteriore, è destinato ad aumentare lo slittamento fino a fermarsi del tutto: per portare al massimo la forza di strappo il cingolo metallico è insuperabile e per tale motivo viene largamente impiegato nel movimento terra.
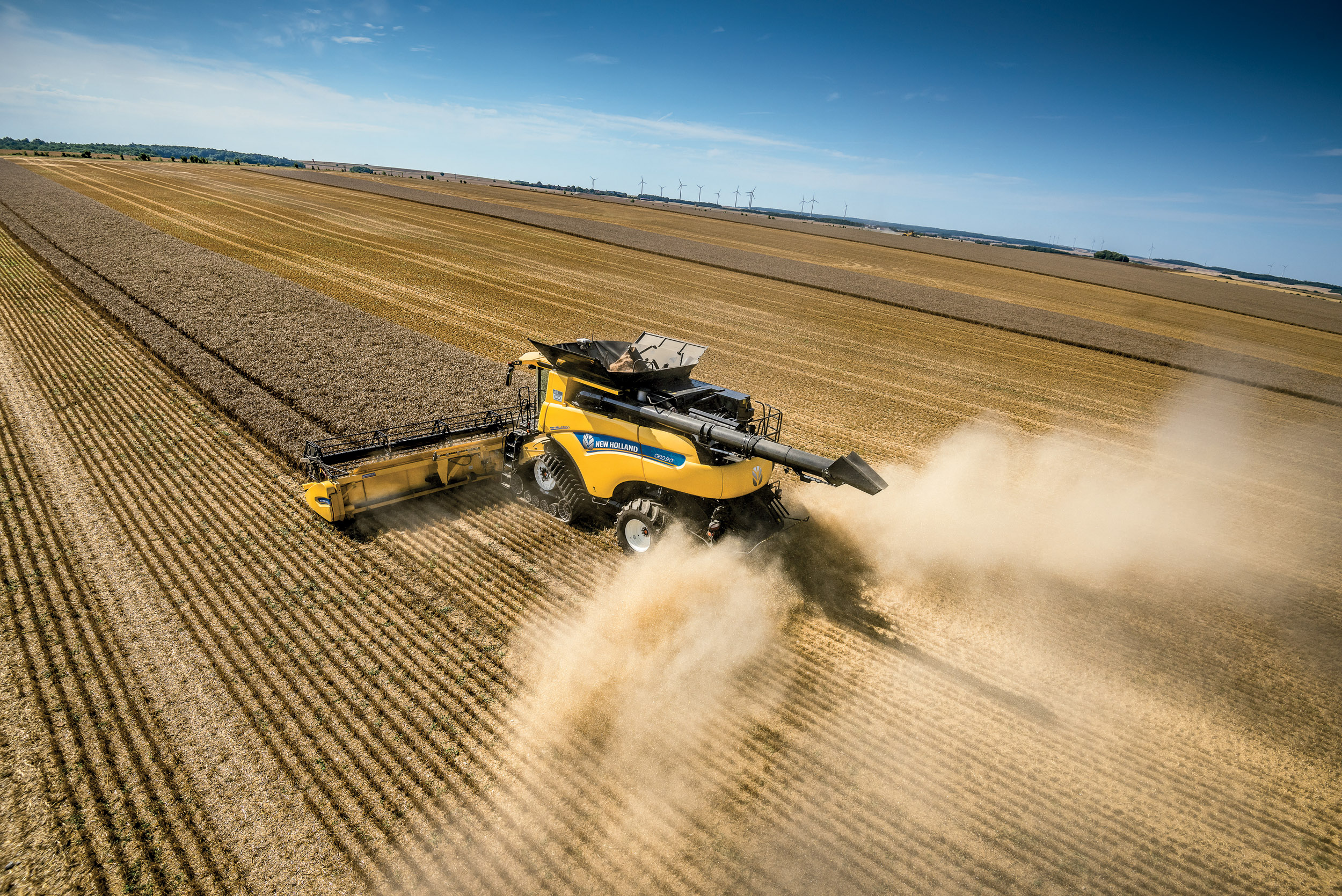
Trazione
Il cingolo di gomma, dal punto di vista della trazione, è assai più simile a uno pneumatico che a un cingolo metallico, nonostante lo sforzo sia sempre proporzionale alla lunghezza del carro.
Rispetto a una ruota pneumatica la superficie di appoggio è considerevolmente superiore con prestazioni più costanti in relazione al tipo di fondo, a differenza degli pneumatici a bassa pressione che richiedono l’aumento della stessa quando vengono impiegati su strada. La ruota gommata ha caratteristiche complementari, riuscendo a sviluppare un soddisfacente sforzo di trazione anche se il carico non è proporzionato alla sezione aderente, nel senso che lo sforzo di trazione si ripartisce fra gli assi (entro certi limiti, quel che si perde davanti si recupera dietro).
L’elevata flessibilità della carcassa, vantaggiosa in campo e su fondo naturale perché consente di adattarsi al profilo superficiale e di scaricare a terra un peso maggiore, si rivela un handicap su terreno duro e alle velocità di trasferimento. La flessione e l’estensione richiedono un lavoro – facilmente verificabile se si prova a trainare il veicolo in folle – che si traduce in calore: più i cicli sono frequenti (aumento della velocità) più calore si genera e deve essere smaltito.
Per quanto la gomma consenta un certo riscaldamento – esiste anzi una temperatura ottimale, come ben sanno i motociclisti – oltre un certo limite si va incontro a una rapida usura del battistrada, fino a danneggiare i cavi che costituiscono la struttura della carcassa. L’usura è legata anche allo slittamento longitudinale e trasversale: quest’ultimo si rende particolarmente evidente nelle gomme a sezione molto larga, il cui lato esterno si trova a percorrere, nei tratti in curva, una traiettoria più lunga rispetto a quello interno. Per quanto possa essere rigida la struttura, è questo il lato più sollecitato, per l’inflessione dell’asse, del sistema flangia-cerchione e della carcassa dello pneumatico: l’accelerazione centrifuga non è sufficiente a scaricare dinamicamente la ruota interna, come avviene negli autoveicoli.
Sul lato meno caricato si manifesta pertanto un certo slittamento, che ha un effetto abrasivo sul battistrada e ne aumenta il consumo, determinando quelle anomalie di usura verificabili sugli pneumatici che vengono usati molto su strada. Quando prevale l’impiego su fondi duri si dovrebbero scegliere pneumatici con carcassa più rigida, a sezione inferiore e con un disegno del battistrada in cui i “pieni” prevalgono rispetto agli intagli. Per contro, quando il veicolo deve essere impiegato soprattutto in campo, è necessario ridurre il carico per unità di superficie, per disturbare il meno possibile il terreno agrario.
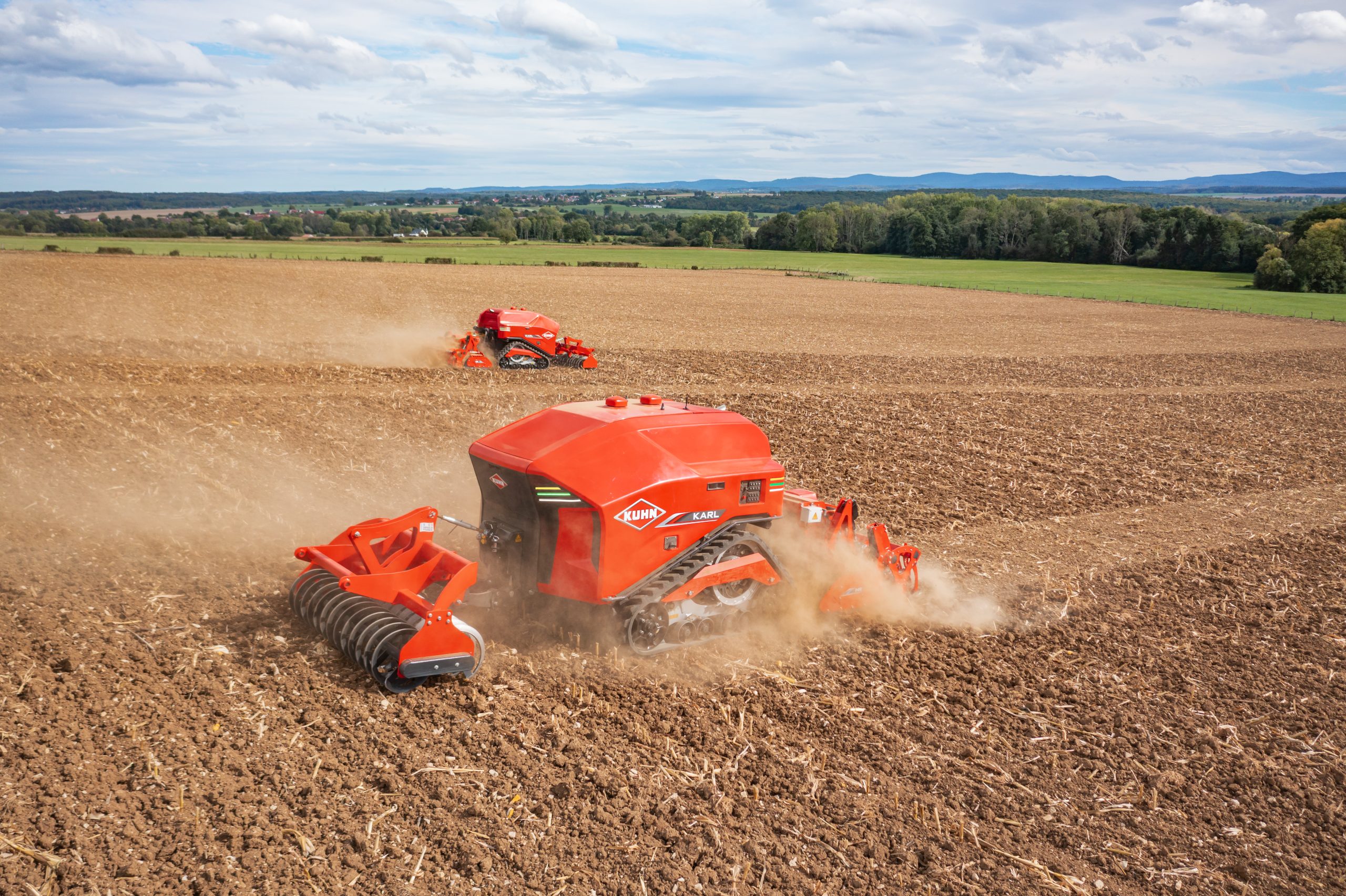
Terreno
La portanza di un terreno è legata a una serie di fattori, come la tessitura (diametro medio delle particelle minerali, minore per le argille e maggiore per la sabbia), alla struttura (aggregati naturali o determinati dalle lavorazioni), ma soprattutto al contenuto in acqua. Questa si comporta come un lubrificante rispetto alle particelle terrose, che scorrono le une sulle altre riducendo lo sforzo necessario per spostarle e quindi per deformare il terreno sotto il peso della ruota o del cingolo: in queste condizioni, la riduzione del carico unitario è fondamentale. Con un suolo argilloso e umido il carico di deformazione del terreno è minimo, inferiore a 0,5 kg per centimetro quadrato: un carico di 1.500 kg per ruota richiede un’impronta di 3.000 cmq, ottenibili con un’impronta di cm 60 di larghezza per 50 di lunghezza (pneumatici “terra tyre”). Non è facile determinare la superficie esatta: bisognerebbe sollevare la macchina con una gru, calarla a terra e poi spostarla (sollevata) per misurare lunghezza e larghezza di appoggio. Dividendo per la misura della superficie (in cmq), avremo il carico medio in kg/cmq; un dato approssimato perché la pressione al suolo è maggiore nella fascia centrale e minore alle estremità. Più semplicemente, il carico unitario si può stimare moltiplicando la larghezza nominale della gomma (la cosiddetta “corda) per la lunghezza di contatto con il suolo, con un coefficiente di riduzione minore per gomme a bassa pressione con profilo piatto e maggiore per quelle standard.
Per le macchine destinate a lavorare con la coltura in atto, non potendo allargare la sezione della gomma si tende ad aumentarne il diametro, come per le irroratrici, ma senza esagerare. Se il peso per ruota supera la portanza del terreno, si deve rinunciare alle gomme strette e tornare alle gomme a sezione larga: dove esiste il rischio di danneggiare la coltura si possono dedicare due corsie al passaggio delle ruote, secondo la tecnica del “traffico controllato”. Questa tecnica è poco utilizzata, almeno in Italia, perché obbliga a unificare la carreggiata di tutti i veicoli che lavoreranno su quel campo; dovendo garantire una buona stabilità trasversale, la larghezza del veicolo potrebbe rendere difficili i trasferimenti su strada.
Da qualche anno i cingoli in gomma sono stati proposti anche su macchine trainate, proprio per evitare l’impiego di pneumatici troppo larghi pur assicurando il massimo galleggiamento sui terreni cedevoli o su quelli interessati da minime lavorazioni o regime sodivo permanente. Il concetto di cingolo “portante”, più che “di trazione”, sembra essere troppo avanzato per la nostra mentalità, tenendo conto del fatto che le annate veramente umide non sono poi così frequenti e che è ancora preferito il carro tandem a due o più assi.
Pressione
Nonostante l’esistenza di numerose soluzioni innovative, i sistemi per la regolazione della pressione degli pneumatici – maggiore su strada e minore in campo – non godono ancora di grande diffusione, soprattutto per i lunghi tempi di adeguamento in relazione alla frequenza di impiego. La crescente produttività oraria delle macchine e la fittissima maglia poderale, rimasta costante da decenni, aumentano l’incidenza dei tempi di trasferimento su quello complessivo di lavoro: il sistema di regolazione della pressione dovrebbe avere una risposta estremamente rapida. In altri paesi – in Europa e non – il trasferimento è meno frequente, ma più lungo e qualche minuto di adeguamento rende più conveniente la regolazione della pressione di gonfiaggio: meno usura e minori consumi su strada, riduzione dello sforzo di trazione fuori strada. Le gomme non pneumatiche restano invece confinate, almeno per ora, alle macchine da cantiere, perché la struttura reticolare, per quanto flessibile, non ha ancora superato quella pneumatica: il secolo in più di storia, di sviluppo e di innovazioni fa ancora sentire i suoi effetti.