Sempre più grandi, sempre più potenti, sempre più produttive. Le mietitrebbie, al pari dei trattori, sono impegnate in una corsa senza freni che le ha portate ormai oltre i 700 cavalli di potenza. A far compagnia in questo segmento alle varie CR New Holland, X9 John Deere X9 e Claas Lexion 8000 avremo, dalla prossima campagna, anche le AF di Case Ih, presentate in occasione di Eima 2024, dopo che ad Hannover, nel 2023, era stata mostrata la nuova 260, erede della 250 AFS, da cui si differenzia essenzialmente per l’elettronica.
Mentre nei padiglioni della fiera bolognese una AF 10 si lasciava fotografare da curiosi e appassionati, la sorella minore, AF 9, mostrava il suo valore su un terreno di prova difficile come la raccolta di mais in alcune delle più produttive zone d’Italia, dove le rese superano regolarmente i 150 quintali per ettaro e saprebbero mettere alle corde anche la mietitrebbia più agguerrita. Un vero stress test, insomma, che il Contoterzista è in grado di raccontarvi in anteprima, avendo seguito la AF in una giornata di prove a Centallo, provincia di Cuneo, su un mais da quasi 190 q/ha. Prima, tuttavia, facciamo una rapida panoramica sulle (molte) novità di una serie che, sono parole di Case IH, nasce dal classico foglio bianco.
Ripartiti da zero
Il progetto, ci spiegano infatti dalla filiale italiana del marchio, è totalmente nuovo, sebbene mantenga il principio che da sempre distingue le mietitrebbie Case IH, ossia la trebbiatura assiale mono-rotore. Quasi un marchio di fabbrica per questo costruttore, che da sempre ne sostiene i pregi. Evidenti, a suo dire, non soltanto negli Stati Uniti, per i quali la trebbiatura assiale è stata inventata, ma anche nella Vecchia Europa.
Partiamo però dalla struttura. Il telaio è largo 1,8 metri, 25 cm in più rispetto alle Axial Flow della serie 260. Aumenta anche la lunghezza del rotore, in modo da avere maggior superficie di separazione. E non parliamo di decimali: mentre le già performanti Axial Flow arrivano a 2,7 metri quadrati, le AF superano i 5 m: praticamente il doppio. A sostenere una simile capacità di lavoro troviamo un Iveco Cursor: 13 per la AF 9, 16 per la AF 10, per un totale, rispettivamente, di 625 e 775 cavalli di potenza massima. Solitamente bastano questi dati a chiudere il capitolo dedicato al motore. Non in questo caso, tuttavia, dal momento che gli ingegneri di Case IH hanno cambiato parecchio in questo comparto. Per prima cosa, la collocazione: il 6 cilindri da 13mila cc è posto in senso longitudinale, come sulle trinciacaricatrici. In questo modo, spiega il costruttore, si ha un rinvio diretto al rotore, senza perdite di potenza dovute agli ingranaggi. Innovativa anche la collocazione dei radiatori: dietro al serbatoio della granella. Posizione che, assicurano i progettisti, è molto più riparata dalla polvere. Inoltre, la ventola del radiatore, in questo modo, tiene pulito il motore poiché soffia aria verso l’esterno della macchina.
Raccolta e trebbiatura
Percorriamo ora il tragitto che fanno i cereali dal campo al serbatoio granella. Le testate, ovviamente, sono proporzionate all’enorme potenza disponibile. Si va, ci dicono i tecnici Case IH, da un minimo di 13,7 fino a 15 metri e oltre per il grano. Misure che rendono praticamente obbligatoria l’adozione della barra a tappeti. Per il mais, invece, si va dalle 12 file in su, con punte financo eccessive come le testate da 16 file montate sulla AF10 al lavoro in Centro Europa. Dove, tuttavia, le rese per ettaro sono ben diverse da quelle italiane.
Dalla barra il prodotto passa al canale elevatore Extra Heavy Duty, con catene rinforzate e funzione cvt a richiesta: grazie a essa è possibile variare in modo infinito la velocità delle catene, adattandosi molto meglio, per esempio, all’azione di uno spannocchiatore.
Gli aspetti più interessanti della gamma AF si trovano però nel sistema di trebbiatura. Il quale resta assiale – Case IH tiene a ribadire che la AF è una macchina Axial Flow a tutti gli effetti – ma guadagna un preparatore, sistemato tra il canale elevatore e l’imbocco del rotore. Il rullo Sfs (Sincronized Feeding System) fa quello che sulle Afs tradizionali fa il cono del rotore, ovvero aiuta il prodotto a entrare nel sistema di separazione e pulizia. Sfs, che lascia parecchio spazio tra esso e l’imbocco del rotore, favorisce dunque il passaggio del prodotto dal canale elevatore al rotore stesso, aumentando la produttività e riducendo il carico di lavoro – e quindi l’assorbimento di potenza – da parte del rotore, grazie anche alla sincronizzazione dei giri i due dispositivi.
Il rotore è come sempre il cuore del sistema Axial Flow. Il salto di qualità, per le AF 9 e 10, è nettissimo. Sulla serie 250 – e la successiva 260, fondamentalmente identica – troviamo un rotore in versione Small o Large (il primo per cereali a paglia, il secondo per mais e soia), diviso in quattro moduli: due di trebbiatura, due di separazione, per un totale di 2,7 metri quadrati. Le AF 9 e 10 hanno un rotore a sei moduli (due di trebbiatura, quattro di separazione) con una superficie di 5,1 metri quadrati: praticamente doppia rispetto alla serie inferiore. La differenza sta sia nella lunghezza, che sfiora i 3,7 metri, sia nella forma: mentre i rotori della serie 260 sono coassiali, quello delle AF maggiori è disassato nella sezione di separazione, in modo da lasciare più spazio al prodotto nella parte superiore. Questa specie di ventilazione naturale, spiegano i progettisti, favorisce la caduta della granella durante la trebbiatura dei cereali a paglia. Per facilitare il passaggio dai segmenti di trebbiatura a quelli di separazione è stata inoltre modificata la spirale del rotore e sono state aggiunte delle barre tra le due componenti del sistema Afs.
Pulizia, scarico, residui
Novità importanti anche sul fronte della pulizia. E non poteva essere altrimenti, per aver ragione della gran quantità di granella che il rotore, ben alimentato da testata e canale elevatore, scarica sui crivelli. Per venirne a capo, i progettisti li hanno raddoppiati: quattro in tutto, con due gruppi crivellanti e due coclee di elevazione, oltre naturalmente al recupero. Per la pulizia abbiamo dunque due crivelli sotto ventilazione, che indicativamente riescono a trattare fino al 60% della granella, cui se ne aggiungono altri due per un totale di 8,8 metri quadrati, utili a completare il lavoro di pulizia e gestire l’eccezionale produttività delle AF 9 e 10 garantendo al tempo stesso perdite pari a zero. O quasi. Innovativo anche il sistema per la gestione del prodotto, basato su quattro sensori di pressione, che riescono a informare il sistema elettronico sulla quantità di granella presente nel cassone crivellante e sulla sua disposizione all’interno dello stesso. Poiché due sensori sono collocati nella parte anteriore del cassone e due in quella posteriore, la differenza di pressione rilevata permette di capire se la macchina rischia di perdere granella dai crivelli e di intervenire con le opportune correzioni di ventilazione o distribuzione del prodotto. Inoltre, il sistema elettronico è in grado di correggere l’assetto dei crivelli quando individua un accumulo di prodotto su un lato piuttosto che sull’altro. «È come se il sistema si auto-proteggesse per evitare perdite dovute a eccessiva ventilazione o a un carico eccessivo di prodotto», ci dice Massimo Sala, responsabile per le macchine da raccolta in Case IH Italia.
Completiamo infine il percorso del prodotto con immagazzinamento e scarico dei residui. Al primo pensa il serbatoio-cereale, che per la AF 9 ha una capacità di 16mila litri (20mila sulla AF 10). Grazie a una coclea che riversa sul carro fino a 159 litri per secondo, si vuota in meno di due minuti. Assai interessante anche la gestione della paglia, nel caso si utilizzi il trinciapaglia. Collocato all’uscita del rotore oppure esternamente, sulla cuffia, è dotato di un doppio sensore radar che legge sia la larghezza sia l’uniformità di distribuzione, ottimizzandole anche grazie a una paratia mobile, che amplia o riduce il raggio di spargimento.
Auto-settaggio
Quando arrivarono anche in Italia i primi sistemi di auto-settaggio delle impostazioni di lavoro, i puristi della trebbiatura li snobbarono bellamente. Con qualche ragione: erano infatti ancora piuttosto grossolani e dovevano essere spesso corretti. Da allora tanta granella è passata per le coclee e i software per l’automazione delle mietitrebbie hanno appreso dagli errori, diventando molto più efficienti e precisi. «Sebbene sia ancora possibile impostare manualmente le nostre macchine, io credo che difficilmente si possa far meglio di Harvest Command, una soluzione che ha al primo posto, nella lista dei vantaggi, la sua semplicità», commenta Sala. Il sistema, spiega, non chiede all’operatore di prendere decisioni in merito a ventilazione, crivelli o altro, ma semplicemente di indicare qual è il valore accettabile di perdite e rotture, oltre naturalmente al tipo di prodotto che si sta trebbiando. «Ottenute queste semplici informazioni, Harvest Command imposta le varie velocità – avanzamento, ventola, rotore – e poi apertura dei crivelli e posizione delle alette della gabbia, per ottenere la massima produttività rispettando i parametri impostati dal conducente».
Lo fa, spiega Case IH, anche grazie a soluzioni esclusive (e brevettate) come una green cam che analizza il prodotto non soltanto in luce visibile, ma basandosi anche su infrarosso, ultravioletto e luce blu, per evidenziare meglio la presenza di impurità – che appaiono nello spettro del verde – e rotture (visibili grazie al colore bianco della cariosside spezzata). «Sistemi come questo, unito al cassone dotato di quattro sensori di pressione e al sofisticato algoritmo che analizza tutte le informazioni, permettono di massimizzare la resa riducendo a zero o quasi perdite e rotture».
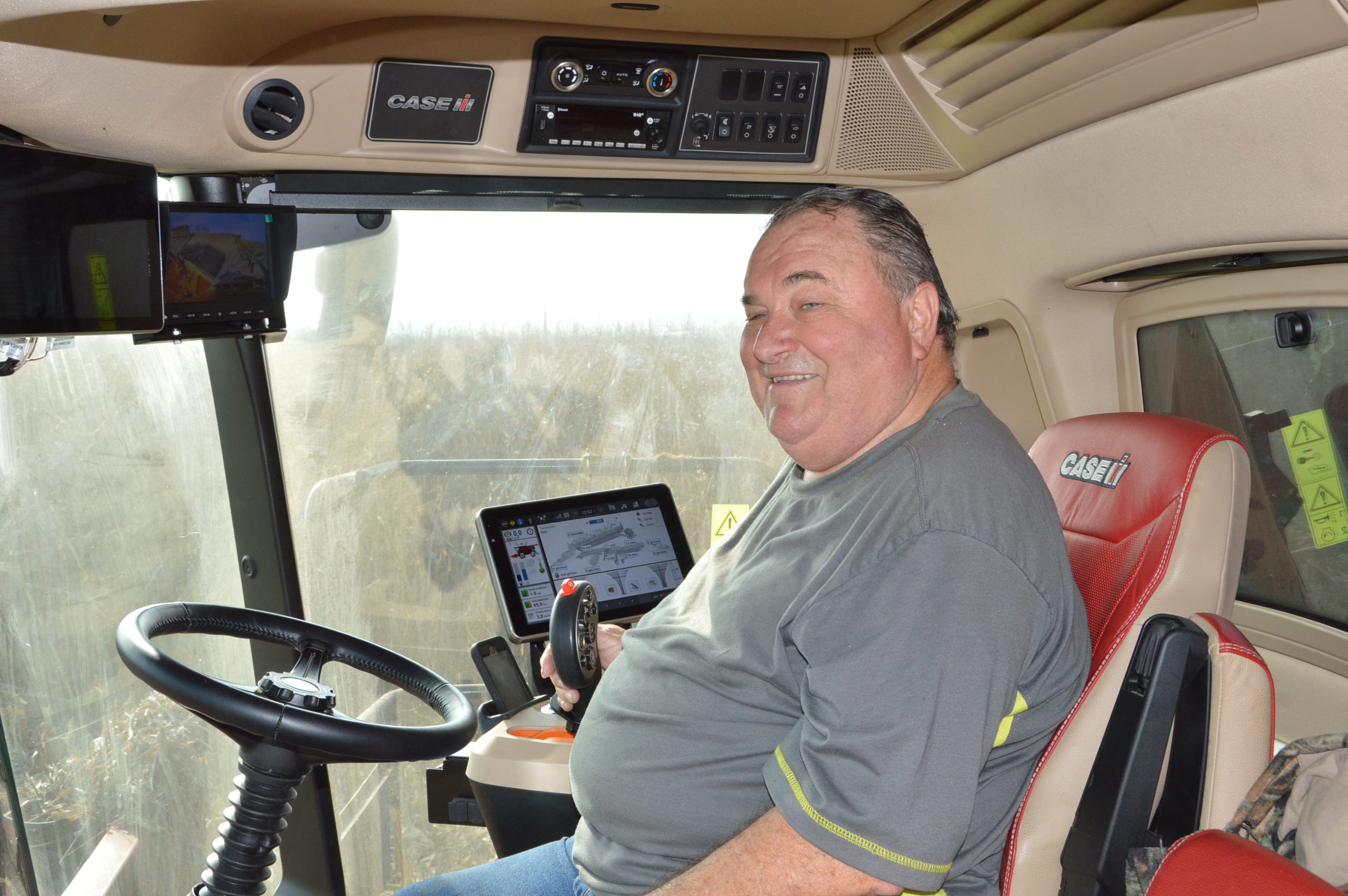
La prova del campo
Come anticipato, abbiamo potuto seguire un test di raccolta realizzato da una delle macchine-prova che nel 2024 hanno girato l’Europa trebbiando grano, soia, girasole e naturalmente mais. L’area scelta da Case IH Italia è stata la provincia di Cuneo, dove non è insolito trovare record produttivi. Qui, ci dicono, la AF 9 ha raccolto mais da oltre 190 q/ha e lo stesso appezzamento trebbiato durante il nostro test era oltre le 18 tonnellate per ettaro.
La raccolta è stata effettuata con una barra da 12 file Case IH, che unita al sistema trebbiante potenziato ha permesso di lavorare al ritmo di circa 120 tonnellate di mais per ora di lavoro, con una velocità approssimativa di 4,5 km/h. Eccellenti le impressioni dalla cabina: la macchina è ben insonorizzata e il sedile principale offre un comfort di tutto rispetto. Buoni anche i volumi dell’abitacolo e l’organizzazione dei comandi, con un doppio terminale che permette di tenere sotto controllo tutti i parametri di lavoro e visualizzare le immagini delle telecamere, una delle quali controlla lo scarico. Valida anche la leva multifunzioni, in grado di controllare quasi completamente la macchina. Del resto, nel caso si utilizzi l’impostazione automatica Harvest Command, le cose che restano da fare al conducente sono, oggettivamente, poche.
La nuova AF convince insomma per capacità oraria e comfort di lavoro. È indubbiamente una mietitrebbia pensata per fare altissime produzioni e da ciò derivano anche i (pochi) ostacoli che possiamo immaginare per il suo impiego nel nostro Paese. Il principale è ovviamente la dimensione, che la rende più adatta alle estese pianure dell’Est Europa che ai piccoli appezzamenti della campagna italiana. Nonostante la maneggevolezza, sicuramente da elogiare, muoversi su strade vicinali di ridotte dimensioni non dev’essere affatto facile. Il sistema trebbiante potrebbe inoltre soffrire la ridotta lunghezza dei campi italiani, dal momento che le assiali, come noto, necessitano di essere ben caricate per lavorare al meglio. Ma è anche possibile che il nuovo preparatore Sfs eviti questo inconveniente, aiutando a ingolfare (in senso buono) il rotore fin dai primi metri, così come sembra rappresentare un’arma vincente per il lavoro con prodotto umido. Un tempo bestia nera delle assiali, ma che oggi, grazie al progresso tecnologico e ai tanti accorgimenti adottati, non spaventa più.